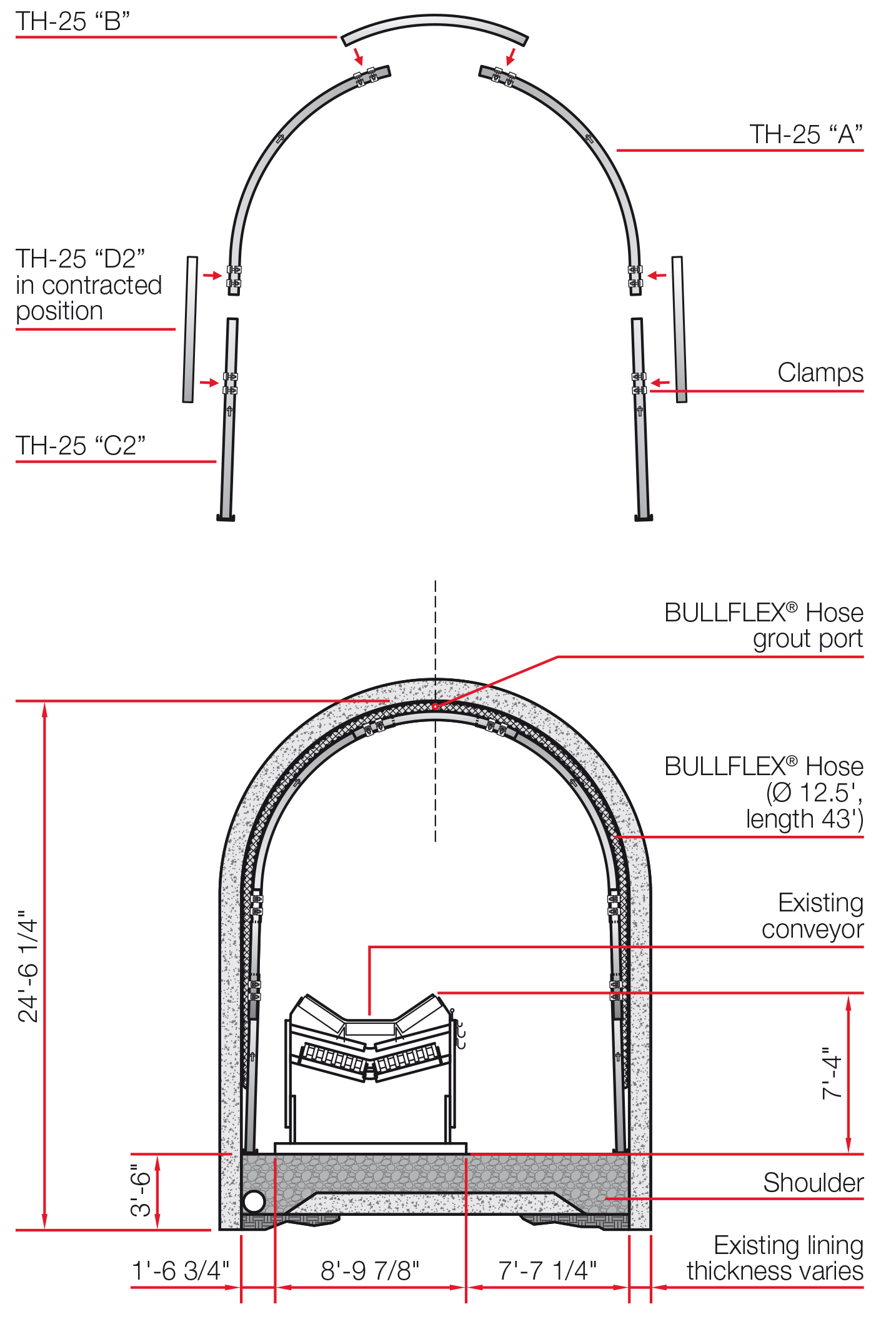
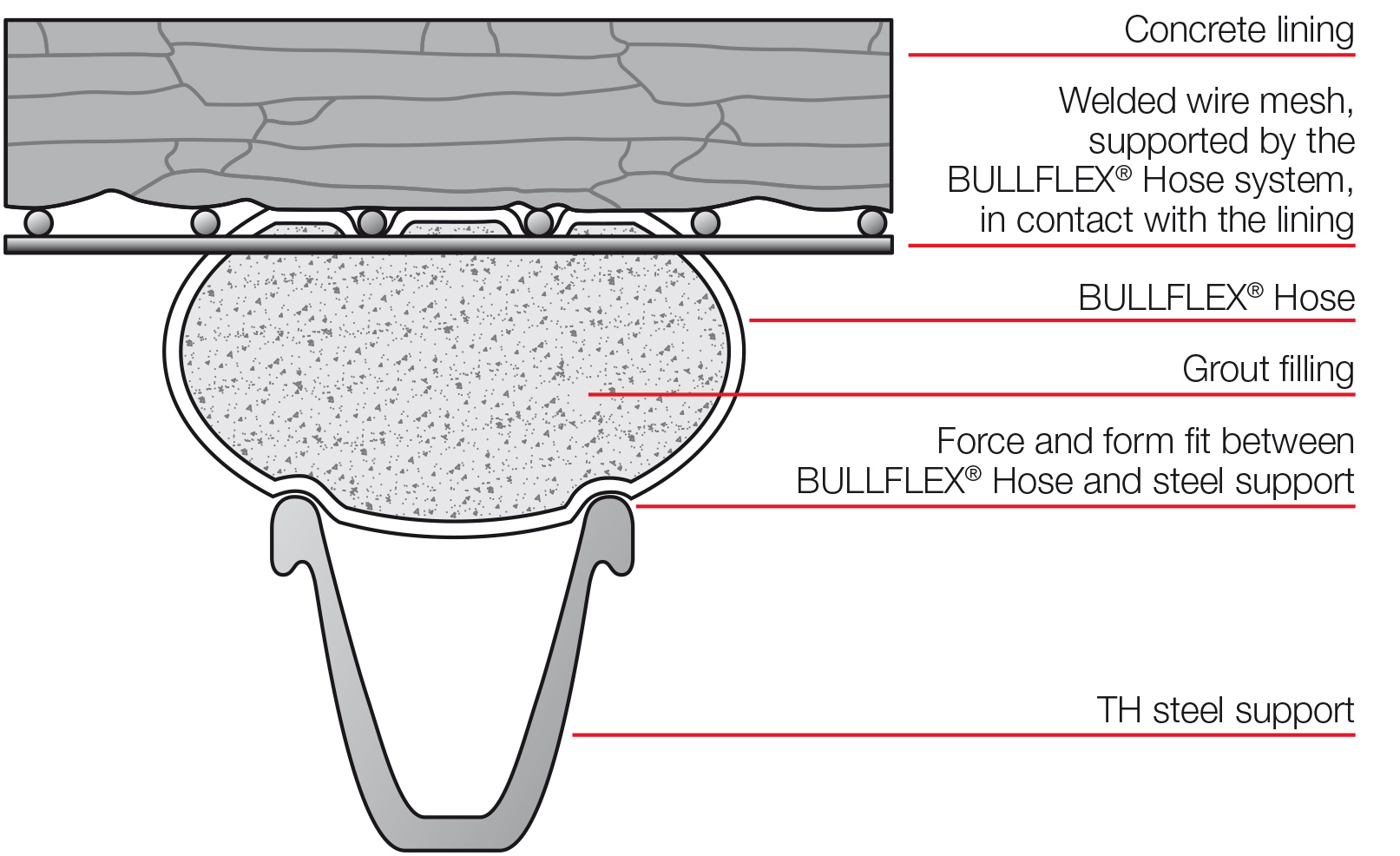
Development and Application of a flexible Combined Support System for Tunnel Rehabilitation
A rehabilitation concept for tunnels consisting of a combination of yielding steel arch sections and BULLFLEX® Roof Support Backfill Hoses was developed and successfully implemented in the course of the rehabilitation of a conveyor tunnel in operation at the Rio Tinto Kennecott Utah Copper (RTKC) Bingham Canyon Mine (Utah, USA).
The focus of the rehabilitation was the approx. 4.5km long C6 conveyor tunnel, which was originally excavated in 1959 as a 5.5 x 7.5m cross section railroad tunnel, and which is currently being used as the main conveyor tunnel. At the time, horseshoe shaped steel sets with a spacing of 1m to 2m were installed as ground support. Furthermore, roof bolts and a timber lagging (200m per tunnel meter) were installed and subsequently backfilled. In addition, load distribution structural elements were selectively used as support for the steel sets in the tunnel invert. Finally, a 25cm to 30cm thick cast in place concrete lining was installed which has since been repeatedly repaired on a provisional basis in the course of time using rock bolts, mesh and shotcrete.
At the beginning of 2014, as a result of nearby open pit mining activities, considerable damage was detected in the C6 conveyor tunnel especially near fault zones. This included severe damage of the concrete lining as well as a clear increase in displacement of the tunnel tube. The damage led to a partial closure of the tunnel so that the urgently required inspection and maintenance work at the main conveyor belt could no longer be carried out. Therefore, a short-term rehabilitation of the affected sections was required without hindering the operation of the conveyor belt.
DSI Underground Systems, Inc. (DSI) and their cooperating partner BuM Beton- und Monierbau GmbH (BuM) were asked to provide technical planning criteria by the engineers Gall Zeidler Consultants LLC (GZ), who had been awarded the contract for developing the rehabilitation concept. In the shortest possible time, DSI and BuM supplied the required information needed to design an efficient and safe rehabilitation concept. Important aspects during the dimensioning of the rehabilitation elements included the fact that the installed support measures had to ensure sufficient clearance, while the impact on the operation of the conveyor belt during the rehabilitation had to be minimized.
Furthermore, a system with immediate loadbearing capacity was needed that ensured a high degree of flexibility in case of increasing convergence. Within a few days, GZ proposed a rehabilitation concept to the customer RTKC and the rehabilitation project was immediately commissioned by the client.
Upon the recommendation of GZ, BuM and DSI, the following stabilization concept was chosen:
- TH steel sets with yielding locks in areas of overlapping segments, Types TH-25 and TH-29
- BULLFLEX® Groutable Hoses functioning as a roof support backfill, 3,200mm Ø
The TH system was developed in the 1930s in Germany for application in highly converging ground conditions in coal mining. The single, interleaved TH sections are connected by lock systems. Depending on number and type, these locks can accommodate a defined load until a controlled slippage of the segments into each other occurs, thus ensuring the yielding ability of the system. For dimensioning of the yielding support system for the C6 Rehabilitation project, in-situ measurements carried out in German coal mining were used as references.
The BULLFLEX® System, which is filled with grout at a pressure of up to 4 bar, ensures a stable and safe form fit between the steel support and the rock. Furthermore, point loads are voided and premature relaxation movements are minimized. Thanks to the special filter effect of the BULLFLEX® fabric, any surplus water is immediately drained, thus maintaining the induced pre-load, i.e. the active support.
The main characteristics and advantages of this combined support system can be summarized as follows:
- Steel arch support with yielding lock systems
- Easy adaptation of the steel support to uneven excavation surfaces
- Controlled slippage in converging ground conditions
- Immediate, full face load bearing capacity and introduction of an active pre-load thanks to the installation of the BULLFLEX® System
The TH steel arch support sections were manufactured at DSI’s plant in Louisville including the load distribution profiles and flexible footings (also known as Dutchmen) in accordance with the design specifications. The steel arch segments and locks were assembled outside of the tunnel and then transported to the underground jobsite using a support manipulator. The Installation was carried out from an elevated work deck using a second support manipulator. The BULLFLEX® Groutable Hoses were filled on site using a grout mix (portland cement and fly ash) supplied by mobile mixing units. In addition to this support system, wire mesh and rock bolts were installed.
The described rehabilitation concept including the combined support system was implemented quickly and successfully. Consequently, the C6 conveyor tunnel is now once again fully accessible and can be considered as stable for the medium term. In cooperation with the customer, Rio Tinto, the mining service provider Cementation and the responsible engineers GZ, DSI and BuM have made an important contribution to restoring the functionality of a drift that is critical for mine operation.